A Brief History of VNA Trucks
The Very Narrow Aisle Trucks (VNA Truck) are a battery-operated machine that uses the electric engine, battery, and operator compartment to counterweight heavy loads. VNA Truck typically uses a wire guidance system to control steering within an aisle allowing the operator to concentrate on moving pallets in and out of racking. The TSP Series VNA truck features a stronger mast, higher reach, and narrow footprint; allowing you to make the most of your storage space. Crown’s exclusive MonoLift mast provides the stability needed for operators and loads up to six floors in the air. The MonoLift mast includes strengthened boxed-in sections and heavy-gauge steel.
The first ‘Man-down’ Very Narrow Aisle (VNA) machines were developed and launched by the Raymond Corporation in the USA in 1949, this niche product only gained minimal initial traction. In 1972 a German based manufacturer Hermann Roehrs Gmbh designed and developed a new solution where the operator was lifted with the load, allowing both pallet placement and retrieval in conjunction with picking and order assembly. This solution has become known as either a VNA Kombitruck, VNA Turret Machine or Man Up VNA.
Hermann Roehrs Gmbh have sold this solution under the Magaziner brand name since 1973. Over that time the company has built a stellar reputation for best in class, custom built Very Narrow Aisle forklift solutions, offering higher lifts and significantly more residual capacity than the competition.
Equipment Guidance
From the early days of VNA truck development in aisle guidance was generally mechanical in nature i.e. the in aisle position of the truck was maintained by a rail installed either side of pallet racking, the VNA truck was supplied with side guidance rollers which maintained the truck in a straight line while travelling along the narrow aisle.
We still see many customers in the UK that have a long history of VNA use and consequently have a preference for rail guided equipment. Mechanical guidance was preferred historically due to the lack of reliability of the very first ‘inductive’ or wire guided systems.
With the development of inductive guidance systems by manufacturers such as Keltronic and Zapi the reliability issues associated with the very first iterations of wire guided systems were addressed and improved upon. Over time the wire guided solution has become more common amongst our customer base both in Ireland and the UK.
Wire guided systems are driven by a closed loop frequency circuit which automatically controls the steering of the VNA truck while operating in the aisle with the inductive wire guidance system plugged in. A frequency generator is installed on the wall of your warehouse, from this position a diamond tipped concrete saw is used to cut a channel down the middle of each racking aisle, returning to this point to complete the circuit, this channel is then backfilled with sealant to protect the wire underneath from wear and tear.
Once the frequency generator is turned on, the wire guidance system is operational. When the operator engages the inductive system, the truck begins to automatically search for the signal that the line driver emits through the wiring loop, when it recognises the signal it automatically adjusts the steering to take up a position in the middle of the aisle, were the truck to lose connection with the signal it will shut down the travel and traverse function of the machine.
Safety Interlocks
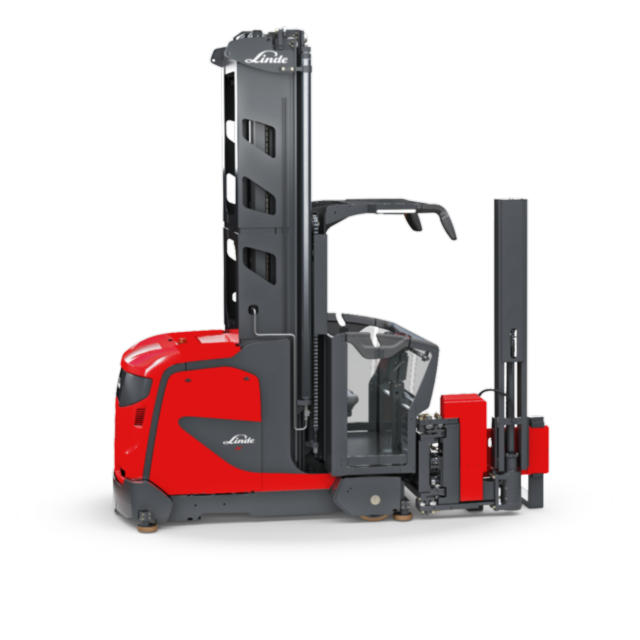
Safety is a key consideration with VNA truck operation, Magaziner can offer a mix of solutions to facilitate a safe system for you and your operation. The main safety interlocks are as follows:
Two hand operation
Vna Truck
In order for the truck to operate the driver must have both hands on the operation controls in addition to placing one foot on the deadman pedal, located on the floor of the operator cabin.
Slowdown & Stop at Aisle End
This feature allows automatic engagement of a slowdown and stop system at the top and bottom each aisle. A number of proximity switches are triggered as the truck travels along the aisle, as these switches are activated the truck automatically slows down and stops at both ends of the aisle.
Zone Dependent Interlocks
A system such as this limits the extended height of the truck as required by the specifics of certain areas of your warehouse space. A system of this nature may be required due to the location of HEVAC, sprinklers or any other overhead obstructions.
Van Truck
Laser Safety Scanner
For busy customer operations that see significant warehouse traffic , we often supply a SICK scanning unit with our Magaziner VNA equipment. Systems such as this continuously scan the surrounding areas, to both the front and rear of the machine, with laser scanners. Should the system detect an obstruction in the general vicinity of the machine (within 4m) the truck will automatically stop in order to prevent a collision.
Reversing Buzzer
Audible alarms are great from a safety perspective, however, the existence of this safety measure may impact upon the drivers productivity, some drivers have at times disconnected this type of an alarm due to the annoyance factor.
Blue Safety Light
More recently we have been fitting front and rear pointing blue safety lights to our equipment, the added advantage of a system such as this is that it does not make any annoying noises while ensuring that your machinery is fully safety compliant.
Operators of Very Narrow Aisle Equipment can :
· Significantly reduce your operating aisle width requirement (can be as narrow as 1400mm, but depends on pallet dimensions) due to the trilateral or turret head that is fitted to the machine – this head rotates through 180 degrees allowing pallet placement both left and right of the aisle without the need to turn to a parallel position with the pallet racking as per a traditional forklift (circa 4 metres) or reach truck (2.9 metres).
· Remove the possibility and costs associated with racking damage – due to in aisle guidance.
Van Truck Game
· Remove the possibility of pallet or load damage - operator is at same level as the pallet.
· Benefit from higher load handling capacities at heights of up to 19 metres, when compared to other solutions.
· Future proof your warehouse operation with the possibility of Semi Automatic and fully autonomous solutions now or in the future.
· Utilise every pallet position can act as a pick face for order picking purposes
· Benefit from increased speed of operation as fewer machine movements are required when compared to reach trucks or other alternatives
Van Truckload
Talk to us today on :
+353 1 8665620/+353 85 8619001
#safetyfirst
#nothingbeatsamagaziner
#thenarrowaisleguys
Quickly and safely around the narrow aisle warehouseVna Forklift
High throughput rates and particularly safe handling processes in the most limited space – Linde Material Handling has designed its turret trucks and vertical order pickers specifically to meet the demands of narrow aisles. This includes powerful drive and lift engines that enable the forklift to move off and lift at the same time, so that the required location in the racking is reached quickly.
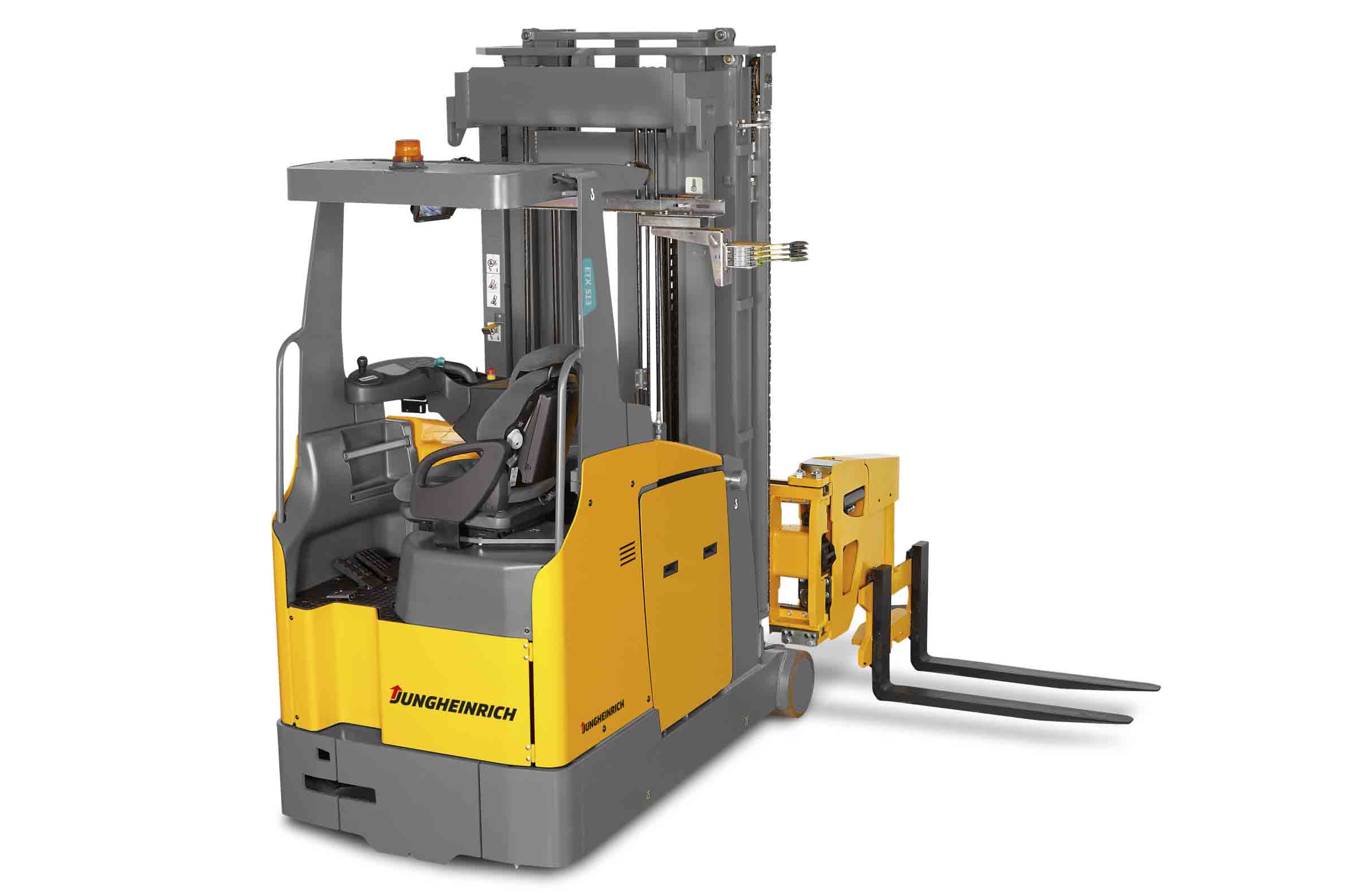
At the same time, the Linde System Control regulates the lift and driving speed according to the weight of the load, optimizing performance according to the driving conditions. Optional Linde assistance systems protect against accidents and assist with rapid navigation through the warehouse. Energy recovery during braking and lowering the load saves energy costs and increases availability. Dependent upon the model and configuration, the lifting capacity can reach up to 1500 kilograms.
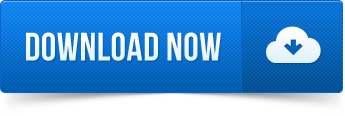